What Are The Different Types Of Plug Valves?
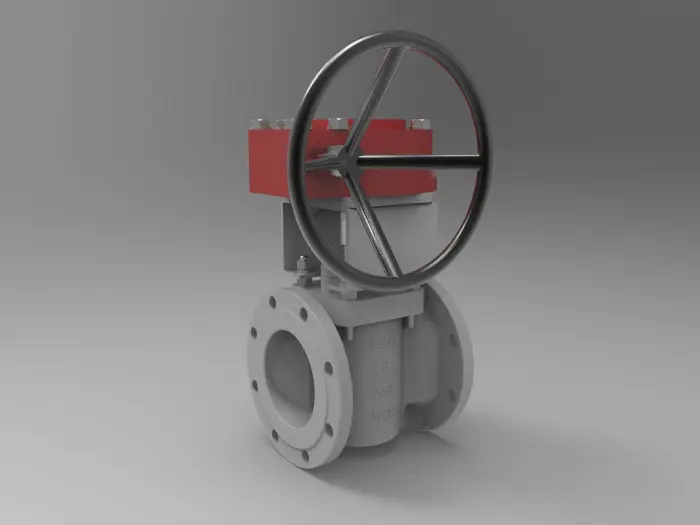
In industrial fluid handling systems, timing, regulation, and shutdown of flow are vital. Plug valves offer durable, tight-sealing flow control to manage liquids, gases, and slurries across myriad sectors. With simplicity and customization, they bring reliability and versatility to fit specific needs.
In this article, we’ll survey common plug valve varieties, inner workings, strengths, and usage scenarios. Whether seeking robust performance, dead-tight shutoff, or specialty alloys, the right configuration exists.
- Oil drain plug valve excels in on/off and throttling roles via straight-through flow control
- Sleeve, inverted pressure balance, flanged, and other types suit varying needs
- Custom alloys and linings handle corrosive, abrasive, high temp media
- Specialized designs meet niche applications like powder handling
By matching attributes to operational duties, plug valves confer superior operability and service life.
Types of Plug Valves
Eccentric plug valves come in a variety of configurations to suit different pressure, temperature, corrosion, and operating requirements. Let’s overview some of the most common valve plug types and their notable attributes.
1. Sleeve Plug Valves
This simple and economical design sees widespread use for relatively low pressure on/off and throttling duties. A cylindrical or tapered plug rotates inside a sleeve to provide tight shutoff without excessive torque. Sleeve valves reliably handle fluids and gases to 175°F and 500psi.
Construction options include carbon steel, stainless steel, alloy steels, and cast iron. For corrosive services, linings and seals of PTFE, UHMW-PE, and various elastomers resist chemical attack. Their moderate cost and versatility make sleeve plugs a workhorse across industries.
- Working Principle – Rotating cylindrical or tapered plug redirects fluid flow perpendicular to seal off port
- Purpose – Moderate pressures, variety of fluids
- Symbol – Rotating cylindrical plug
2. Inverted Pressure Balance Plug Valves
In larger sizes and higher pressure/temperature services, inverted pressure balance plug valves shine. Their distinguishing feature is a pressure-balancing piston isolated from the flow media by a bellows seal. This balanced design requires little actuation force, even on large valves.
By inverting the plug, flow enters the higher body section. This subjects the plug to line pressure on both sides to avoid becoming pressure bound. Such valves provide bubble-tight shutoff on liquids, gases, and vapors to 1500psi and 1400°F, with exotic alloys handling far greater extremes.
- Working Principle – Inverted plug & pressure balance piston allow easy actuation under high pressures
- Purpose – Tight shutoff for gases & liquids at high pressures
- Symbol – Plug & bellows or piston
3. Orbit Plug Valves
The orbit plug valve uses an eccentric rotating disc to incrementally vary flow across a 175° sweep, enabling precise flow regulation. Their modulating control makes orbit valves well-suited for looping flow paths.
Available in carbon steel or stainless steel bodies to suit process needs, these valves have live-loaded packing, making them ideal for throttling applications involving frequent operation. Extended plug stem designs allow for automated actuation and remote control capabilities.
- Working Principle – Eccentric rotating disc incrementally regulates flow across 175° range
- Purpose – Precise throttling, loop system regulation
- Symbol – Off-center disc
4. Flanged Plug Valves
For large port sizes, high-pressure applications, and easy integration with pipe infrastructure, flanged plug valves fit the bill. Face-to-face dimensions match gate and globe valve standards, enabling interchangeability.
Both regular and lined configurations suit temperatures from -320°F to 1000°F. Choices of screw-in, welded, and bolted bonnets enable customized dismantling access and tight shutoff. With power actuators, these robust valves operate reliably even at pipeline pressures.
- Working Principle – Scalable, flanged construction enables tight shutoff at high pressures
- Purpose – Large pipelines, interchangeable with gate/globe valves
- Symbol – Bolted bonnet
5. Twin Seal Plug Valves
Mission-critical services demand robust shutoff redundancy. Twin seal plug valves deliver with two packing seals above and below the valve port. This double protection prevents hazardous leakage in the event of a single seal failure.
The twin seal’s tandem barrier allows hot swapping of the upper seal under line pressure. Constructed of stainless steel and high alloys, these duty valves handle fluids and gases from -100° to 750°F, with metals and soft seats handling up to 1400°F.
- Working Principle – Double seal barriers provide leak-proof redundancy
- Purpose – Zero-leak critical processes
- Symbol – Dual horizontal seals
Stainless Steel Plug Valves
Where superior corrosion and oxidation resistance are needed, stainless steel delivers. Types 304 and 316 stainless constructions resist chemical attack across applications like chemical processing, salt water exposure, and washdown service.
With no protective coating to wear away, stainless steel valves maintain material integrity. Their polished surfaces prevent fluid residue adhesion and biological film growth. While costlier than carbon steel, stainless pays off in longer service life and reduced maintenance.
- Working Principle – Corrosion resistant metals withstand demanding services
- Purpose – Corrosive chemicals, pharmaceuticals, food
- Symbol – “SS” material designation
PANS | Plug Valve Manufacturers
With over 35 years specializing in industrial valves and pipeline components, PANS brings quality and versatility to flow control applications. As a fully integrated manufacturer based in China, PANS handles product development, material sourcing, machining, assembly, testing, certification and sales under one roof.
The product range covers Various types of plug valves, gate, globe, ball, check, bellow valve designs, complemented by strainers, fittings, flanges, and pipes. Rugged metal constructions spanning carbon steel, stainless steel, bronze, nickel alloys suit an array of demanding services. Extensive in-house production capability allows customized valves to meet unique customer specifications.
Through integrated manufacturing and quality assurance, PANS delivers reliable components to prominent Chinese infrastructure projects and export clients worldwide. Companies seeking a proven valve supplier can count on PANS for application-matched flow control solutions backed by three decades of manufacturing expertise.
Conclusion
Plug valves remain a versatile workhorse across industries needing reliable flow control. From basic on/off functionality to precise throttling, their simple yet customizable design meets diverse needs. Sleeve, inverted pressure balance, orbit, flanged, twin seal, and stainless steel configurations all serve specific pressure, temperature, corrosion, and operating requirements.
With 35+ years manufacturing valves and pipelines, PANS has the expertise to deliver customized plug valves and integrated solutions for your application. Contact our engineers today to discuss leveraging plug valves’ strengths for your precise flow control needs.
Search
Categories
Tags
Product
- Ball Valve
- Floating Ball Valve
- Fully Welded Ball Valve
- Trunnion Ball Valve
- Check Valve
- Cast Lift Check Valve
- Cast Swing Check Valve
- Wafer Type Check Valve
- DIN Valve
- DIN Bellow Sealed Globe Valve
- DIN Globe Valve
- DIN Rising Stem Gate Valve
- DIN Swing Check Valve
- Forge Valve
- Forged Check Valve
- Forged Floating Ball Valve
- Forged Gate Valve
- Forged Globe Valve
- Gate Valve
- Bellow Sealed Gate Valve
- Flat Gate Valve
- Wedge Gate Valve
- Globe Valve
- Cast Globe Valve
- Plug Valve
- Eccentricity Plug Valve
- Inverted Pressure Balance Lubricated Plug Valve
- Orbit Plug Valve
- Sleeve Type Plug Valve
- Slurry Valve
- Slurry Valve
- Strainer