What Is The Inverted Pressure Balance Plug Valve?
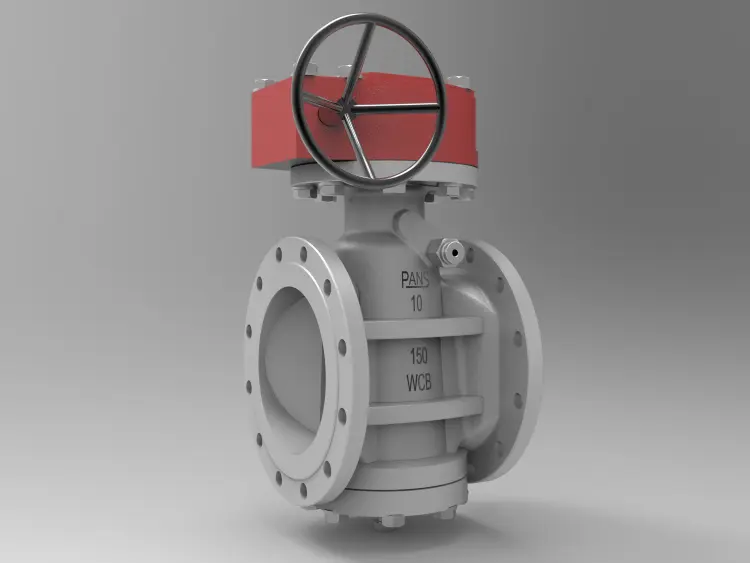
When handling volatile gases, liquids, or multiphase flows in high-pressure applications, safety and reliability are paramount. Inverted pressure balance plug valves enable secure isolation and flow control across pipelines, preventing hazardous leaks under extreme conditions.
- Designed for natural gas, oil, and petrochemical applications with ANSI Class ratings up to 4500
- Pressure-balanced plug seals tighter as line pressure increases
- Inverted configuration protects seat from debris damage
- Limitations include higher initial cost and reduced bore sizes
Inverted Pressure Balance Plug Valve – Overview
Why is it called inverted pressure balance plug valve? Inverted pressure balance plug valves build upon standard lug or wafer plug valve architecture. They integrate a pressure balanced plug to improve shutoff security by forcing the plug harder against the body seat as line pressure rises. This fail-safe ability to seal more tightly under higher loads prevents accidents.
An inverted orientation flips the valve upside down to protect the seats, avoiding the accumulation of sediment and debris on sealing surfaces over long-term operation. Combining this inverted body layout with pressure-balanced plug control enables robust performance and safety across oil & gas gathering, transmission, storage, and distribution systems.
Why is inverted pressure balance plug valve used?
Inverted pressure balance plug valves serve critical functions across high-pressure oil & gas pipelines, storage facilities, and distribution infrastructure. Their enhanced sealing reliability and durability deliver distinct advantages.
1. Secure Isolation Capability
The pressure-balanced plug design compensates for line pressure, enabling reliable shutoff and isolation up to ANSI 4500 ratings. As inlet pressures rise, the offset cammed plug shifts to force the downstream seal harder into the body seat. This self-adjusting action prevents hazardous leaks, securing containment during maintenance or transfers.
2. Resilient Sealing Over Time
Flipping the valve body upside down shields the seats from contact with media. By avoiding the accumulation of sediments, hydrates, scale, or debris on sealing surfaces, the inverted orientation protects against seat erosion and leakage over decades of cycling. This durability ensures public and environmental safety.
3. Withstand Harsh Operating Environments
Inherent to oil & gas systems, inverted pressure balance plug valves[1] handle a breadth of demanding services from wellheads to transmission pipelines, storage terminals to distribution networks. Whether coping with sour multiphase production flows, high-pressure natural gas gathering, or extremes of cycling, temperature, chemicals, or abrasives, the resilient design meets the toughest field requirements.
What is the function of the inverted pressure balance plug valve?
Here are a few functions of inverted pressure balance plug valve:
1. Flow Control and Isolation
Like standard plug valves, inverted pressure balanced models provide precise flow regulation in addition to tight shutoff. Rotating the plug via the actuator varies the orifice opening, throttling flow as demanded by downstream processes. This gives operators proportional control for optimized conditions.
2. Pressure Compensation Across Variable Loads
A precision-machined channel running through the plug creates a balancing area that adjusts in relation to line pressure. As inlet pressure rises, this balancing area transmits loading to the downstream plug face, augmenting the seal.
3. Bidirectional Sealing
Inverted pressure balanced plug valves achieve bidirectional isolation and flow regulation, sealing off pressure equally well from either direction. The symmetrical plug and body configuration shuts off and modulates flow with the same exemplary performance ratings up to Class 4500, regardless of flow orientation.
What is the purpose of a inverted pressure balance plug valve?
Inverted pressure balanced plug valves serve the vital purpose of enabling secure isolation and proportional flow control across high-risk oil and gas transfer systems. Their specialized internal design pursues several key reliability objectives:
- Deliver bubble-tight shutoff up to ANSI Class 4500 ratings, stopping dangerous high-pressure leaks even during pressure spikes or fluctuations.
- Maintain strong, consistent sealing over decades of cycling. Flipping the valve body upside down prevents corrosive contaminants and debris from accumulating on the seats. This erosion resistance retains long-term integrity.
- Regulate flow rates with precision as conditions vary. The pressure-balanced plug automatically shifts to increase downstream sealing force as inlet pressure rises. This self-compensating capability stabilizes flow control.
- Withstand exposure to abrasive liquids and gases, temperature swings, contaminants and other harsh pipeline environments. Rugged alloy materials and components withstand these demanding services.
- Operate with lower torque requirements than alternatives like gate or ball valves, saving actuation effort and system wear.
- Achieve bi-directional sealing performance across reversing or intermittent flows, with equivalent metrics in either orientation. Symmetry enables versatile installations.
What are the limitations of inverted pressure balance plug valves?
While inverted balanced plug valves offer refined safety and performance over standard options, there are some limitations to consider:
1. Higher Initial Costs
The complex manufacturing and precision machining required for pressure-balanced plug components come at a premium price. Inverted balanced plug valve units have significantly higher initial procurement costs compared to basic plug, ball, and gate valves.
2. Size Constraints
Currently, inverted balanced plug valves only scale up to a maximum bore size of 18 inches. Their intricate inner mechanisms pose design barriers when trying to expand to larger pipeline diameters. By comparison, some slab and expanding gate valves service pipes over 48 inches.
3. Maintenance Expertise
Though durable, inverted balanced plug internals have more intricacy requiring specialized service technicians for repairs. Their pressure balance mechanisms also demand careful calibration. Most operations lack this high-level expertise in-house.
4. Compatibility Factors
Flow media properties like viscosity, solids content, and crystallization temperature can impact function. Thorough application inspection is advised when specifying these valves for production fluids.
PANS – Inverted Pressure Balance Plug Valve Supplier
As a premiere valve engineering firm founded in China in 1985, PANS specializes in applying the latest materials and patented designs to improve industrial flow control safety. Leveraging over 30 years of expertise, the company manufactures high-quality plug, gate, globe, ball, check, and specialty valves to global energy markets.
By integrating intelligent R&D, precision manufacturing, and rigorous testing, PANS provides long field-life safety and productivity for customers operating high-risk, sensitive processes. Clients worldwide trust their exceptional quality inverted balanced plug valves to prevent leaks and maintain control.
Conclusion
Whether coping with extremes of pressure, temperature, abrasives, or cycling, inverted pressure balance plug valves furnish reliable flow control where leakage prevention is paramount. PANS leverages 30+ years perfecting sleeve and trim innovations to supply exceptionally durable, customized designs.
Their integrated R&D and manufacturing applied across plug, gate, ball and specialty designs drive energy infrastructure advances worldwide. Contact PANS engineering experts today.
Search
Categories
Tags
Product
- Ball Valve
- Floating Ball Valve
- Fully Welded Ball Valve
- Trunnion Ball Valve
- Check Valve
- Cast Lift Check Valve
- Cast Swing Check Valve
- Wafer Type Check Valve
- DIN Valve
- DIN Bellow Sealed Globe Valve
- DIN Globe Valve
- DIN Rising Stem Gate Valve
- DIN Swing Check Valve
- Forge Valve
- Forged Check Valve
- Forged Floating Ball Valve
- Forged Gate Valve
- Forged Globe Valve
- Gate Valve
- Bellow Sealed Gate Valve
- Flat Gate Valve
- Wedge Gate Valve
- Globe Valve
- Cast Globe Valve
- Plug Valve
- Eccentricity Plug Valve
- Inverted Pressure Balance Lubricated Plug Valve
- Orbit Plug Valve
- Sleeve Type Plug Valve
- Slurry Valve
- Slurry Valve
- Strainer