How To Grease A Plug Valve?
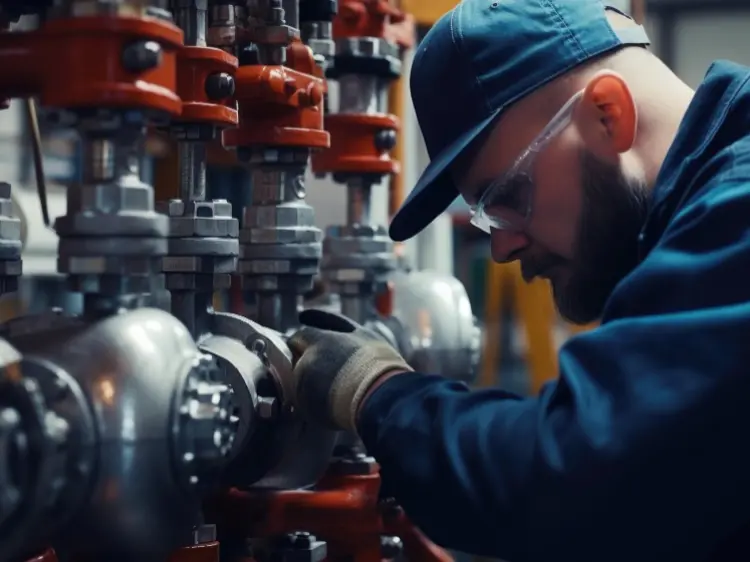
Plug valves provide reliable flow control across demanding industrial and infrastructure applications. Like other moving parts, occasional re-lubrication maintains ease of operation and prevents wear.
- Plugs and stems enable quarter-turn on/off control
- Routine lubrication reduces friction, extends part life
- Grease plug valves every 6-18 months, depending on the use
- Confirm smooth operation post-greasing
- Grease ports, plug seals are key lubrication points
In this guide, we’ll overview plug valve anatomy, proper greasing steps, testing, FAQs, and work with PANS to customize valves to your needs.
Anatomy & Operation
The signature plug valve consists of a valve body, plug, and stem[1]. The cylindrical or tapered plug fits inside the body bore. As the plug rotates 90°, it redirects flow from fully open to fully closed.
Machined plug geometry provides tight shutoff without flow restrictions. The plug connects to an upper stem that rotates it via a handle, gearbox, or automated actuator. Together, the moving plug and stem enable reliable throttling and shutoff.
Where lubrication factors in:
Surfaces between the plug and body can experience high friction during cycling. Periodic re-lubrication here and on seals reduces torque needs and ensures smooth action. This prevents excessive wear that allows leaks or makes valves hard to operate.
How To Lubricate A Plug Valve?
Here’s a step-by-step guide on how to grease a plug valve:
- Identify lubrication points
These include grease fittings on valve bonnets or stems, and plug seal surfaces. Some plugs feature hollow cavities to hold grease internally.
- Select compatible grease
Use lithium or calcium thickened base greases rated for valve application temperatures. Avoid incompatible greases containing solvents or corrosive compounds.
- Add grease
Apply grease gun to fittings. Remove plug seals first if present and lightly coat sealing surfaces with fresh grease before reinstalling. Replace seals if wear is evident.
- Cycle valve
Turn the plug fully open to closed several times post greasing to evenly distribute lubricant. Extra cycling helps purge any trapped air pockets.
- Inspect operation
Plug rotation should move smoothly without stick-slip or high effort. Tight shutoff without leakage should occur on both sides of plug in closed position.
- Document maintenance
Note grease brand and amount used. If issues are discovered, record details to determine if future adjustments like seal replacement are needed.
PANS | Plug Valve Suppliers
PANS manufactures high-quality plug valves for industrial applications across China and worldwide export clients. With integrated in-house operations from R&D to production to sales, PANS engineers valves matched to your pressure, media, and operation requirements.
Leverage three decades of experience supplying specialized plug valves configurable with alloys, linings, and automation. Contact PANS to explore customizing durable plug valves for optimized functionality.
Search
Categories
Tags
Product
- Ball Valve
- Floating Ball Valve
- Fully Welded Ball Valve
- Trunnion Ball Valve
- Check Valve
- Cast Lift Check Valve
- Cast Swing Check Valve
- Wafer Type Check Valve
- DIN Valve
- DIN Bellow Sealed Globe Valve
- DIN Globe Valve
- DIN Rising Stem Gate Valve
- DIN Swing Check Valve
- Forge Valve
- Forged Check Valve
- Forged Floating Ball Valve
- Forged Gate Valve
- Forged Globe Valve
- Gate Valve
- Bellow Sealed Gate Valve
- Flat Gate Valve
- Wedge Gate Valve
- Globe Valve
- Cast Globe Valve
- Plug Valve
- Eccentricity Plug Valve
- Inverted Pressure Balance Lubricated Plug Valve
- Orbit Plug Valve
- Sleeve Type Plug Valve
- Slurry Valve
- Slurry Valve
- Strainer