What Is A Sleeved Plug Valve?
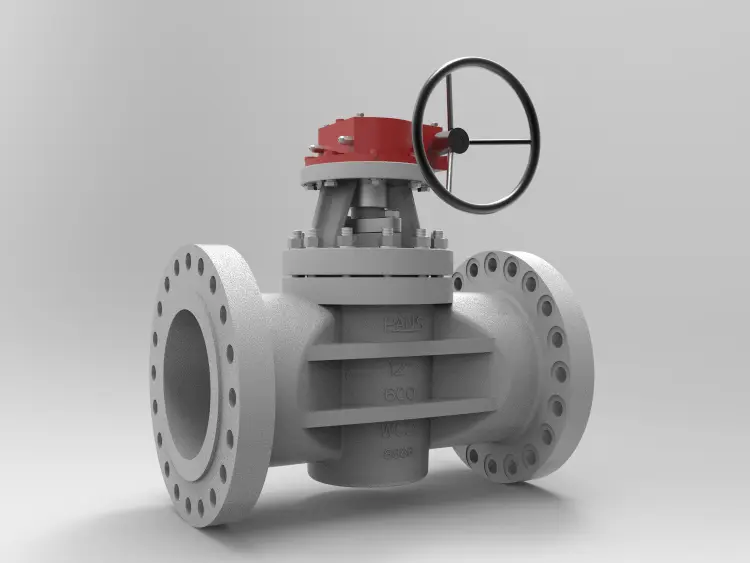
Used in thousands of industrial flow control applications, sleeved plug valves provide reliable on/off and throttling control over time. But what exactly are they and what sets them apart from other valve designs?
- Sleeved plug valves route fluid through a cylindrical sleeve
- The sleeve protects the valve body from wear and erosion
- This extends service life compared to standard plug valves
- Applications range from corrosive chemicals to abrasive slurries
- PANS leads the industry in sleeved plug valve innovation
Sleeved plug valves might look similar to standard plug valves on the outside, but inside they contain a very different flow control element. Instead of routing fluids directly through the valve body, a removable cylindrical sleeve protects interior surfaces. This gives sleeved plug valves unique advantages in demanding services.
Sleeved Plug Valve Overview
Like pipelines themselves, most valves have interiors sized for the desired flow capacity. Sleeved plug valves add a replaceable sleeve to this flow path through the valve body. Typically made of corrosion-resistant alloys, sleeves channel process fluids.
The sleeve allows inline inspection and replacement when worn without having to cut welding flanges or replace the entire valve. This advantage over standard plug valves makes sleeved versions ideal for abrasive flows that erode surfaces over time. Their customizable liner materials also handle corrosion.
How does a sleeved plug valve work?
A sleeved plug valve works by rotating a plug inside the valve.
When opening, the plug lifts slightly to reduce wear. The plug aligns with the flow path to allow fluid through, while the sleeve provides a tight seal.
When closed, the plug blocks the flow, ensuring no leakage.
The key innovation that makes sleeved plug valves unique is the addition of a removable, replaceable cylinder along the flow path – the sleeve. Here are the key operating components:
1. Sleeve
Typically made of wear and corrosion resistant materials like stainless steel or exotic nickel alloys, the sleeve acts as a liner through the valve body. It provides a smooth flow conduit.
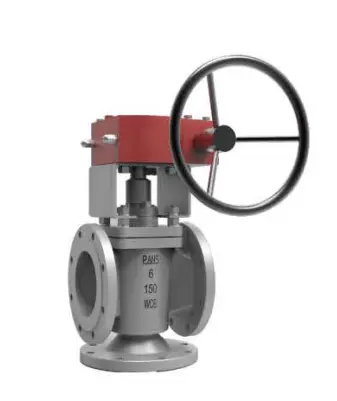
2. Plug
The plug is a cylindrical flow control element with a flow passage bore. Rotating it perpendicular to the bore opens and closes the valve. The outer plug surface forms a tight seal with the sleeve.
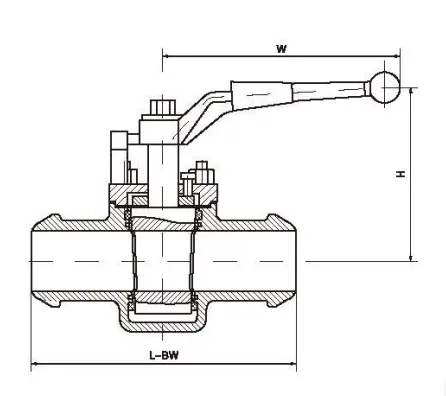
3. Body Seals
High integrity seals on both sides confine process fluids within the valve, keeping hazardous or volatile substances from escaping to atmosphere.
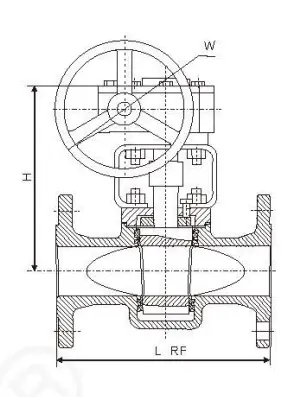
4. Stem & Bearings
An upper stem connects to the plug below, allowing rotation via manual handle or automated actuator. Stem bearings enable smooth movement.
What is the purpose of a sleeved plug valve?
By adding sacrificial and customizable sleeves, sleeved plug valves reliably throttle and shut off fluids across a wide array of demanding industrial services:
What is the function of a sleeved plug valve?
- Corrosive Chemicals: Suitable sleeve alloys resist corrosion even from acidic flows.
- Abrasive Slurries: Sleeves prevent internal gouging and erosion from particulates.
- Frequent Cycling: Rotary control handles hundreds of thousands of cycles.
- Throttling Duty: Plug bore designs fine-tune restrictive flow regulation
- Positive Isolation: Tight shutoff seals hazardous fluids without leakage
Liner replacement restores full flow capacity and avoids having to remove complete valves from the line. This unique benefit makes sleeved plug valves ideal choices for pulp & paper plants, chemical refineries, food & beverage, wastewater, mining, and other challenging applications.
What is the application of a sleeved plug valve?
With their heavy-duty construction and field-replaceable sleeves, sleeved plug valves reliably handle fluids in the most demanding industrial environments. Here are some of their leading applications.
1. Corrosive Chemical Flows
Acids, caustics, solvents, and corrosive catalysts rapidly eat away at standard valve materials. Sleeved plug valves install corrosion-resistant sleeve alloys like Alloy 20, Hastelloy, and exotic nickel-copper mixes to withstand these services for years. Common applications include:
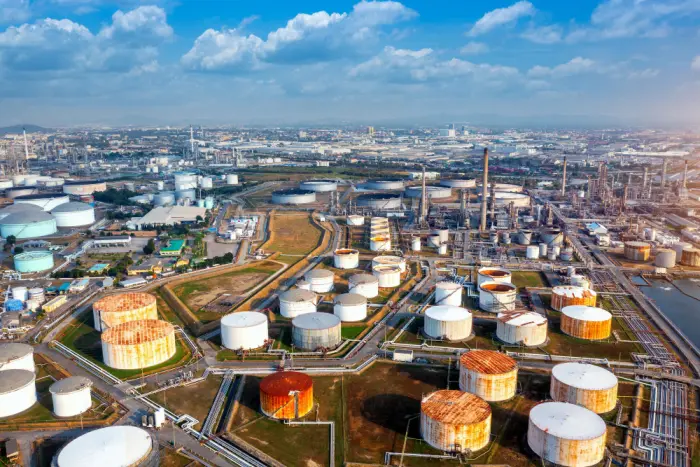
> Sulfuric acid flow control in fertilizer and wastewater plants
> Caustic soda regulation in pulp & paper processing
> Hydrochloric acid isolation in chemical production
2. Abrasive Slurry Handling
From mine sites to ceramic plants, industries deal with high-solids flows that wear away at piping and valves. Sleeved plug valves handle these abrasive slurries with aplomb, channeling the flow through replaceable wear sleeves rather than the valve body. Typical abrasive applications include:

> Mine tailing flows
> Fly ash and pulverized coal transport
> Kaolin and mineral slurries
> Ash handling systems
As sleeve replacement restores full flow capacity, sleeved plug valves outlast standard models by years in abrasive services. Plant operators save time and money by avoiding full valve changeouts.
What is the difference between sleeved and lined plug valves?
While both sleeved and lined plug valves provide wear protection, they utilize different methods to achieve this. The key contrasts between the two designs are outlined below:
1 | Sleeve Construction | Sleeved plug valves incorporate a complete cylindrical removable sleeve that surrounds the entire plug. This sleeve fits into the valve body, providing a replaceable wear surface along the full 360-degree flow path. Constructed of corrosion and abrasion-resistant alloys, sleeves take the brunt of damage from fluids and particulates. Once worn, the sleeve can be easily replaced without disassembling the valve. |
2 | Liner Composition | Lined plug valves instead utilize spray coatings, plastic inserts, or thin overlays in certain regions of the valve body and plug. Because linings do not fully encapsulate components, they cover limited zones off to the side rather than directly in the flow stream. This leaves the main bore unprotected. Reapplying or replacing linings also requires extensive valve disassembly to access covered areas. |
3 | Sleeve Advantages | Compared to linings, sleeves furnish more robust, comprehensive protection along the entire flow path where erosion and corrosion occur. The replaceable sleeve concept also allows for straightforward maintenance to restore full flow capacity and pressure retention, avoiding downtime from complete valve replacement. For longest service life, sleeved plug valve designs excel over lined models. |
PANS – Sleeved Plug Valve Manufacturer
As a premier valve manufacturer based in China, PANS specializes in applying the latest materials and designs to improve industrial flow control equipment. Founded in 1985, the company leverages over 30 years of experience across plug, gate, globe, ball, check, and other valves.
A pioneer as sleeved plug valve exporters, PANS holds numerous patents optimizing sleeve geometries and alloys for demanding applications. Their removable cylindrical sleeve design protects valve bodies from erosion and corrosion in the most challenging oil & gas, chemical, mining, and wastewater services.
By integrating R&D, intelligent design software, precision manufacturing, and comprehensive quality testing, PANS delivers reliable, long-lasting valves to markets worldwide. Customers rely on their innovative sleeved plug valves to handle abrasive, corrosive, and cycling applications that defeat standard designs.
Want to Know More? Request a Quote! >>
Sleeved Plug Valve PDF Download >>
Conclusion
Whether handling abrasive slurries or corrosive chemicals, sleeved plug valves outperform thanks to replaceable cylinder sleeves that protect valve bodies. This innovative method to extend service life makes PANS a leader supplying sleeved designs worldwide.
Contact PANS today to implement sleeved plug valves in your most important or problematic applications.
Search
Categories
Tags
Product
- Ball Valve
- Floating Ball Valve
- Fully Welded Ball Valve
- Trunnion Ball Valve
- Check Valve
- Cast Lift Check Valve
- Cast Swing Check Valve
- Wafer Type Check Valve
- DIN Valve
- DIN Bellow Sealed Globe Valve
- DIN Globe Valve
- DIN Rising Stem Gate Valve
- DIN Swing Check Valve
- Forge Valve
- Forged Check Valve
- Forged Floating Ball Valve
- Forged Gate Valve
- Forged Globe Valve
- Gate Valve
- Bellow Sealed Gate Valve
- Flat Gate Valve
- Wedge Gate Valve
- Globe Valve
- Cast Globe Valve
- Plug Valve
- Eccentricity Plug Valve
- Inverted Pressure Balance Lubricated Plug Valve
- Orbit Plug Valve
- Sleeve Type Plug Valve
- Slurry Valve
- Slurry Valve
- Strainer